Laser cladding
Laser cladding is the process of adding a pure metal or an alloy in its powder form to a new or remanufactured component to protect against wear, corrosion or abrasion. First developed as a heat source for surface engineering technologies in the late 1990s, laser cladding offered a better finish than the contemporary surface engineering techniques – a finish that would deliver even longer component life. It provides customers with access to coatings and overlays with a full metal bond.
Cladability
Cladability is the formation of a continuous, high density clad deposit with a uniform or homogenous microstructure, possessing a strong metal bond to the substrate but with low dilution. However, in particular cases, cladability could also include the requirement of a certain level of dilution by substrate, a certain clad height or deposition efficiency or even specific materials properties that are required from the clad.
Mechanism of cladding
During cladding process enough energy must be delivered by the laser beam to process volume that the powder stream and a small volume of substrate surface melts. Then the liquid phases rapidly mix and become homogenous phases. During the cooling period this well-mixed phase solidifies and forms the basis of the dense well-bonded clad layer (fig 1). The energy delivered to the process is depending of the following parameters such as:
- Laser beam energy
- Spot size
- Velocity of the substrate
- Frequency F
- Duration of the pulse W
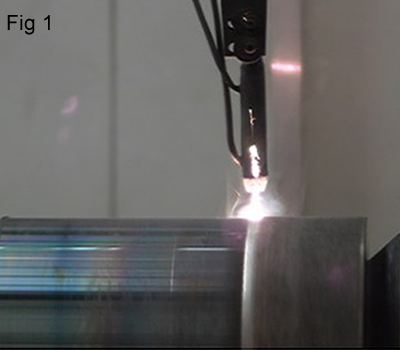
Some advantages
Laser cladding offers many advantages over the aforementioned conventional coating processes. It can deliver a much higher quality of coating, with minimal dilution and distortion, offering enhanced surface quality parameters. The properties of the surface material thus obtained have similar or even better characteristics than originally.
The advantages of laser cladding are such as :
- reduced production time
- enhanced thermal control
- highly satisfactory repair of parts
- Production of a functionally graded part
- Production of smart structures
- No flaking, peeling or cracking
- High accuracy
- Highly repeatable, efficient process
Some Disadvantages
Some distinctive challenges related to the implementation laser cladding technology have been identified. In fact there are very few negative characteristics such as:
- relatively high equipment and running costs
- a lack of knowledge of the technological and financial benefits
- resistance from industry caused by negative past experiences with early, unreliable lasers
- poor acceptance of a potential reduction in manpower
- a need for retraining
- unexplored technical difficulties
Applications
Major application of laser cladding is in the repair and refurbishment of high value components such as tools, turbine blades, gas turbine and internal combustion, engine parts. Its three fields of industrial application are surface cladding, repair welding and generative manufacturing. The process is a reliable macro-materials’ processing technology. One of its primary applications is the deposition of well-known wear-resistant.