Abstracts of some Papers
Production of tungsten via leaching of scheelite with sulfuric acid
H. Razavizadeh, A. Ershad langroudi, MINERALS & METALLURGICAL PROCESSING Vol. 23, No. 2 . May 2006,page 67/72
A new process for leaching scheelite ore consists of leaching low- and high-grade concentrates with H2SO4 in the presence of H3PO4 and NaCl at atmospheric pressure. The resulting tungstic acid solution is then evaporated to produce ammonium paratungstate (APT): (NH4)10H2W12O42.4H2O. To obtain the yellow oxide (WO3), the APT is heated at 600° to 700°C for one hour to evaporate ammonia and water. The reduction of tungsten trioxide with H2 can be controlled by the temperature, time and water vapor partial pressure to produce α-W.
Key words: Tungsten, Scheelite, Leaching
The publication is available at link:SME.com,
SME(MINERALS & METALLURGICAL PROCESSING)
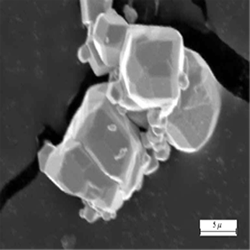
Deoxidizing Copper with CaB6
Hekmat Razavizadeh and S.Mirdamadi.T., JOURNAL OF METALS February 1987 Page 42/47
Copper deoxidizing by elements such as phosphorus and lithium is common in industry, but when copper is deoxidized with phosphorus, leaving residual phosphorus greater than 100ppm electrical conductivity is rapidly reduced. Copper deoxidizing by lithium in industry is not common because of the high cost. If it is carried out, however, it is done after first deoxidizing by phosphorus. This paper attempts to investigate the copper deoxidizing effect by CaB6 and determine the influence of CaB6 on the electrical conductivity and age hardening.
The publication is available at link.springer.com".

Leaching of Sarcheshmeh copper oxide ore in sulfuric acid solution
H. Razavizadeh and M.R. Afshar, MINERALS & METALLURGICAL PROCESSING, Vol. 25, No. 2 . May2008
The recovery of copper from oxide ores containing from 2% to 4.1% acid-soluble copper from the Sarcheshmeh mine in Kerman province of Iran was investigated by agitation leaching in sulfuric acid media. Quartz, as a major constituent, and malachite, as the major copper mineral, were identified in the ore by X-ray diffraction (XRD) and microscopic studies. A series of leaching experiments on the ore was performed over a concentration range of 10 to 20 g/L and temperatures from 15° to 50°C for a maximum of 3 hours. An initial high dissolution of copper was followed by a very slow reaction. By increasing acid concentration and temperature, the dissolution rate of copper was accelerated. However, by increasing acid concentration, the acid consumption of ores was also increased. Surface morphology of solid residues at various leaching times was examined with a scanning electron microscope (SEM). All SEM micrographs of the partially reacted particles displayed a needle structure. The kinetic studies showed that the malachite dissolution rate could be modeled in two stages. About 85% of the malachite dissolution occurred in Stage 1, while the remaining 15% occurred in Stage 2. The data obtained for the leaching kinetics indicate that the dissolution for Stage 1 was a diffusion-controlled reaction with an activation energy of about 20.6 kJ/mole, and the dissolution for the Stag 2 was a chemical-controlled reaction with an activation energy of about 87.6 kJ/mole.
Key words: Copper, Copper oxide, Oxide ore, Malachite, Sulfuric acid, Leaching, Kinetics
The publication is available at link:SME.com,
SME(MINERALS & METALLURGICAL PROCESSING)
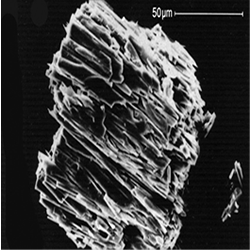
Characterisation of copper anode slimes from Sar-Cheshmeh containing barium sulphate
Hekmat Razavizadeh, Robert Gee, ERZMETAll, 42(1989) Nr.12
The production of precious and other technologically important metals from copper anode slimes is complicated by the many components present in slimes. The precise constitution of the slimes is determined by the original copper ore, the pyrometallurgical processing treatments and the electrolytic refining conditions. At Sar-Cheshmh, the slimes also contain about 50% of barium sulphate which causes considerable extra problems in the recovery processes. The present work provides general information about the Sar-cheshmeh complex and describes a new flotation leaching method for removing barium sulphate from the slimes. This process also enabled the constitution of the slimes to be examined in more detail by scanning electron microscope and X-ray diffraction.
The publication is available at link:World of Metallurgy(ERZMETALL),
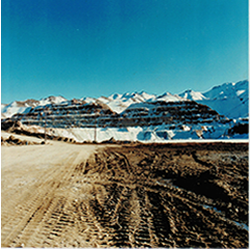
A New Process for Titanium Aluminides Production from TiO2
A.R.Kamaliy, H.Razavizadeh and S.M.M.Hadavi, J. Mater. Sci. Technol., Vol.23 No.3, 2007
This paper describes a new process for producing titanium aluminides, in particular TiAl, from TiO2 raw material. On the basis of obtained results, the non-completed reaction of TiO2 with Al and Ca in a special reaction vessel results in the production of granulates of titanium aluminides especially Ti3Al and other Ti- Al phases as the metallic product and Ca12Al14O33 as the non-metallic product. By adding KClO4 in the mixture, a nearly completed reaction can be carried out. The products of this reaction are titanium aluminide particularly TiAl as the metallic part and CaAl4O7 (grossite) as the non-metallic slag part. Both product and slags are produced in a separated form. This process, called KRH-method is described in this article the scanning electron microscopic microstructure of metallic part of the product shows different phases: the matrix phase is TiAl, where the needle form precipitation is TiAl2 and the plate form precipitation includes TiAl and Ti3Al phases. The microstructure of the remelted metallic part indicates dendritic phase with a lamellar structure comprising of TiAl and Ti3Al phases. The interdendritic phase of TiAl is also seen.
KEY WORDS: Titanium aluminide; Titanium dioxide; Grossite; KRH process
The publication is available at link: jmst.org,
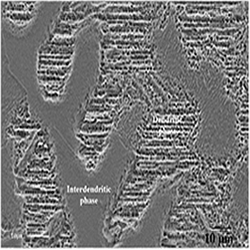
THE LEACHING OF NEZAMABAD SCHEELITE WITH SULFURIC ACID
Hekmat Razavizadeh1,A.Ershad Langroudf,Iranian Journal of Materials Science & Engineering,Vol.I, No.I,2004.
A new process for recovering scheelite ores comprises producing a concentrate from the ore, then leaching the concentrate with H2 SO4 in the presence of H3PO4and NaCl at atmospheric pressure are discussed. Finely purification of the product will be described. The amounts of dissolution of tungsten in acid depend on the parameters such as time, temperature, type and concentration of acid and salt as well as solid-liquid reaction. These factors were optimized for the result and described in details.
Keywords: Tungsten, Nezamabad, Scheelite, Sulfuric acid, Acid leaching
The publication is available at link: Iranian Journal of Materials science and Engineering.com ,
Iranian Journal of Materials science and Engineering
Bacterial leaching of Sarcheshmeh Copper Sulphide Concentrate in the presence of Thiobacillus Ferrooxidans
H.Razavizadeh and A Jafarnia,Journal of Sciences and Engineering vol 15, Nr1, p15/25, 2004(1383) Iran University of Science & Technology
At the present time Bioleaching is one of major areas of research in metal sulphide concentrate. In this paper the bacterial leaching of Sarcheshmeh copper sulphide concentrate with sulphuric acid in the presence of Thiobcillus ferrooxidans (Sarcheshmeh mine (PTCC1647 and DSM583 from Germany ) were investigated to increase the recovery of copper.The chemical composition of the concentrate is 30% Cu,24% Fe and 31%S.The main mineralogical compositions of the concentrate are chalcopyrite, chalcocite and pyrite . The effect of parameters such as pH, pulp density and additives FeS2 were studied .The results indicated that leaching of the concentrate with sulphuric acid led to increase the recovery of copper in the presence of thiobacillus ferrooxidan. This effect was more active using the bacteria from the Sarcheschmeh mine. Finally the results showed that the addition of FeS2 to the concentrate was beneficial in the recovery of the copper
Recovery of Zinc from the Final Slag of Steel's Galvanizing Process
N. Dakhili, H. Razavizadeh, M. T. Salehi, S. H. Seyedein, Advanced Materials Research Vols. 264-265 (2011) pp 592-596
With the rising cost of zinc reaching historic levels, more emphasis is being placed on technologies to increase the efficient utilization of zinc. One area targeted for increased efficiency is in-house recycling of metallic zinc industrial wastes. The largest consumer of zinc is the hot-dip galvanizing of steel. Large amount of zinc slag containing more than 50% zinc, are accumulated during galvanization processes at the surface of molten zinc bath and is usually skimmed manually. At First, The pyrometallurgical recovery of zinc from slag samples was carried out, and parameters affecting recovery processes such as time, temperature, and flux percentage were studied. The results obtained revealed that zinc metal is successfully recovered from these secondary resources. The recovery efficiency is 70% for zinc waste materials having a particle size diameter of + 1.25 mm. An optimum percentage of 25% weight of ammonium chloride fluxing agent was obtained. The optimum temperature for the recovery process was 700 °C.
Key words: Recovery, Zinc, Galvanizing, Slag, pyrometallurgical treatment.
The publication is available at link: Advanced Materials Research, www.scientific.net,
Production of TiAl(Ti3Al)/Al2O3 Nanocomposite
A.R.Kamali, a, S.M.M.Hadavi, J.Baboee, H.Razavizadeh, Journal of Nano Research Vol. 3 (2008) pp 7-14
Titanium Aluminide-based composites withAl2O3 reinforcement can be produced via reaction of Al with TiO2. These composites are considered as low-cost materials for high temperature applications. Addition of KClO4 to the TiO2/Al system was investigated in this research. On the basis of the results obtained, addition of KClO4 to the mixture of TiO2/Al and subsequent heating, results in titanium aluminide/alumina nanometric particle formation with dimensions of about 30 nm. Densification of this composite powder leads to production of a titanium aluminide-alumina nanocomposite body. Dimensions of the alumina phase are in the range of 100-150nm.
Keywords: Titanium aluminide/alumina, Nanocomposite, Thermal combustion
The publication is available at link Journal of Nano Research, www.scientific.net,
Investigation on Fabrication of W-Cu Nanocomposite via a Thermochemical Co-Precipitation Method and its Consolidation Behaviour
M. Hashempour, H.R. Rezaie, H. Razavizadeh, M.T. Salehi, H. Mehrjoo, M. Ardestani, Journal of Nano Research Vol. 11 (2010) pp 57-66
W-25%Cu nanocomposite was produced via a thermochemical co-precipitation procedure. Copper nitrate and sodium tungstate salts were used as Cu and W containing precursors respectively. Aqueous solutions of these salts were reacted under controlled pH condition prepared by ammonia addition and the resulting precipitates were then calcined at 450oC and hydrogen reduced at 800oC. The products of each step were characterized by XRD and Electron Microscope. Using a basic medium with a pH of 13 which caused the formation of complex Cu(NH3)42+ was found to provide suitable condition for precipitation of nanosized composite powders. Cu2WO4(OH)2 and CuWO4.2H2O as raw precipitates, CuWO4-x , CuO, and WO3 as calcined powders, and W-Cu reduced composite powders, all were seen to keep nanosize dimensions through high temperature treatments of fabrication. Sintering of the reduced powders at the temperature of 1150oC led in a density of about 98% theoretical density.
Keywords:W-Cu Nanocomposite, Thermochemical Co-precipitation, Synthesis, Sintering
The publication is available at link Journal of Nano Research, www.scientific.net,
Synthesis of W- Cu- Ag Nanopowders Produced by A Co-Precipitation Process
Golnaz Taghavi, Hamid Reza Rezaie, Hekmat Razavizadeh, Defect and Diffusion Forum Vols. 312-315 (2011) pp 312-318
A homogeneous precipitation process was employed to prepare nanosized W-10%wtCu- 10%wtAg powders using ammonium meta tungstate, copper nitrate and silver nitrate as precursors. The initial precipitates were obtained by reacting ammonium meta tungstate, copper nitrate and silver nitrate solutions under certain pH and temperature. In order to synthesis W-Cu-Ag composite powders, the initial precipitates washed, dried, and then calcined in air in order to prepare CuWO4-x, Ag2W4O13 and WO3 oxide powders for the next step reduction. The reduction was carried out in a hydrogen atmosphere to form the final W-Cu-Ag nanocomposite powders. The powders were characterized by X-ray diffraction (XRD) technique. The morphologies of the powders were observed by scanning electron microscopy (SEM).
Keywords: Nano Materials, W-Cu-Ag Nanopowders, Co-Precipitation
The publication is available at link Journal of Defect and Diffusion Forum, www.scientific.net,
Synthesis of WC–20 wt. % Cu composite powders by co-precipitation and carburization processes
M. ARDESTANI, H. ARABI, H. RAZAVIZADEH, H. R. REZAIE, H. MEHRJOO, Materials Science-Poland, Vol. 28, No. 2, 2010
WC/Cu composite powders were synthesized by co-precipitation and subsequent reduction-carburization process. The precipitates contained W-Cu compounds fabricated using a chemical procedure from a mixture of copper nitrate and ammonium paratungstate in distilled water. In order to synthesize the WCCu composite powders, dried precipitates were calcined at 823 K in air and then reduced and carburized by carbon monooxide (CO). The non-isothermal mechanism of reduction-carburization of the calcined powders in carbon monoxide was investigated by thermogravimetry, differential thermogravimetry and X-ray diffraction analyses. The optimum reduction-carburization temperature was determined as 1065 K. The microstructures of the powders were characterized by the scanning electron microscopy.
Keywords: WC-Cu composites; reduction; carburization; thermogravimetry
The publication is available at link Journal of Materials Science-Poland,
Chemical mechanism of precipitate formation and pH effect on the morphology and thermochemical co-precipitation of W–Cu nanocomposite powders
Mazdak Hashempour,, Hekmat Razavizadeh, Hamid-Reza Rezaie,,Maral Hashempour, Mohammad Ardestani, Materials Chemistry and Physics 123(2010)83–90
W–25%Cu composite powder was produced via thermochemical procedure. Copper nitrate and sodium tungstate salts were used as Cu and W containing precursors, respectively. Aqueous solutions of these salts were reacted under several different pH conditions. It was found that the products of all stages involving Cu2WO4(OH)2 and CuWO4.2H2O as raw precipitates, CuWO4-x, CuO, and WO3 as calcined powders, and W–Cu reduced composite powders possessed similar compositions in different pH conditions. But changing the reaction pH in the range of 3–13 was found to markedly influence the microstructure of the products. At low and medium pH precipitates were in the form of large monolithic agglomerates while in high pH smaller cotton like agglomerates were formed. At low and medium pH conditions simple ion replacement was found to be dominant mechanism of precipitation while in high pH Cu(NH3)42+ complexion was formed and ligand exchange was the dominant mechanism of precipitation.
The publication is available at link Journal of Materials Chemistry and Physics,
Materials Chemistry and Physics
Effect of Ball Milling on Reaction between TiO2 and Al
A. R. Kamali, Babaei Nejad, M. R. Aboutalebi, and H. Razavizadeh, Russian Journal of Non-Ferrous Metals, 2009, Vol. 50, No. 3, pp. 246–249.
Titanium Aluminide based composites with Al2O3 reinforcement can be produced via reaction ofAl with TiO2. These composites are considered as low price materials for high temperature applications. In this research, the effect of ball milling on 3TiO2 /7Al system was investigated. On the basis of obtained results, ball milling for 0 to 60 h does not lead to reduction of TiO2 by Al. but reduces the temperature of exothermic reaction
The publication is available at link Russian Journal of Non-Ferrous Metals,
Russian Journal of Non-Ferrous Metals
Production of Ti-8Al-1Mo-1V Alloy by Using of New Master Alloys
Ali Reza Kamali, S.M. Mehdi Hadavi, Hekmat Razavizadeh,International Journal of Material Science Volume 3, Number 1 (2008), pp. 61–67
Production of a titanium alloy with nominal composition of Ti-8Al-1Mo-1V was studied. Melting of elemental raw materials in an arc remelting furnace under argon atmosphere led to evaporation of aluminum and formation of high molybdenum inclusions. Using of TiAl and Mo3Al8 raw materials led to production of an alloy with acceptable deviation of elements with a microstructure free from inclusions
The publication is available at link International Journal of Material Science,