SUPERALLOYS
Superalloys are alloys that have excellent mechanical strength and creep resistance at high temperatures, good surface stability, and corrosion and oxidation resistance. They typically have an austenitic face-cantered cubic crystal structure with a base alloying element of nickel, cobalt, or nickel-iron. The corrosion-resistant superalloys are widely used in extreme environments where heat and corrosion resistance is better to the integrity of the end product. Chemical and petrochemical processing, power plants, and oil and gas industries widely are used these superalloys.Superalloys are designed to be used at temperatures of 540 oC and higher, typically up to 0.7 x their absolute melting temperature, which may be up to around 1000 oC. At 760 oC most superalloys have yield strength in excess of 500MPa. They are also corrosion resistant. About three quarters of superalloys are used in aerospace; typically about one half of the weight of a modern jet engine is made up of superalloys.
Applications of superalloys are such as:
- Vanes and blades for jet and gas turbine engines
- Heat exchangers
- Components for chemical reaction vessels
- Equipment for heat treatment
Types of Superalloys
There are 3 different types of superalloys as following:
- Nickel-based alloys which form the bulk of alloys produced, are basically nickel-chrome alloys with a fcc solid solution matrix containing carbides and the coherent intermetallic precipitate Y(Ni3(Al1Ti). This latter precipitate provides most of the alloy strengthening and results in useful operating temperatures up to 90% of the start of melting. Further additions of aluminium, titanium, niobium and tantalum are made to combine with nickel in the Y' phase and of molybdenum, tungsten and chromium which strengthen the solid solution matrix. Nickel based - may be wrought or cast. Typically more than 40% Ni, 10-20% Cr, up to 10% Al and Ti, 5-10% Co and small amounts of B, Zr and C. Mo, W and Nb are also commonly added.
As mentioned earlier, creep and oxidation resistance are the prime design criteria. Superalloys can be based on iron, cobalt or nickel, the latter being best suited for aeroengine applications. The essential solutes in nickel based superalloys are aluminum and/or titanium, with a total concentration which is typically less than 10 atomic percent. This generates a two-phase equilibrium microstructure, consisting of gamma (γ) and gamma-prime (γ'). It is the γ' which is largely responsible for the elevated-temperature strength of the material and its incredible resistance to creep deformation. The amount of γ' depends on the chemical composition and temperature, as illustrated in the ternary phase diagrams in figures 1 and 2.
The Ni-Al-Ti ternary phase diagrams show the γ and γ' phase field (Figures 1and 2). For a given chemical composition, the fraction of γ' decreases as the temperature is increased. This phenomenon is used in order to dissolve the γ' at a sufficiently high temperature (a solution treatment) followed by ageing at a lower temperature in order to generate a uniform and fine dispersion of strengthening precipitates..
- The cobalt-base superalloys have been in use for several decades in the manufacturing of various components such as vanes or combustion chambers in gas turbines (both the industrial type and aeroengines). They can be implemented as wrought or as precision-cast parts. Their design is aimed primarily at improving elevated temperature strength by use of solid-solution-and carbide-strengthening mechanisms. Such mechanisms must tolerate substantial additions of chronium (above 20 wt.%) in order to obtain a satisfactory oxidation resistance and a good hot corrosion resistance. Cobalt based - may be wrought or cast. Typically contain 35-60% Co, 20-30% Cr, up to 35% Ni with some W and Mo. Although in terms of properties the (Y’) hardened nickel-based alloys cast and wrought cobalt alloys continue to be used because:
- Cobalt alloys have higher melting points than nickel (or iron) alloys. This gives them the ability to absorb stress to a higher absolute temperature.
- Cobalt alloys give superior hot corrosion resistance to gas turbine atmospheres; this is due to their high chromium content.
- Cobalt alloys show superior thermal fatigue resistance and weldability over nickel alloys.
- Iron-based superalloys are characterized by high temperature as well as room-temperature strength and resistance to creep, oxidation, corrosion, and wear. ... Oxidation resistance increases with chromium content. The martensitic chromium steels, particularly alloy 616, are used for steam-turbine blades. Iron Nickel based is one of the important alloys of this part. These are an extension of stainless steel technology and are frequently wrought. Typically contain 20-40% Ni, 15-20% Cr, 30-50% Fe, plus Mo, Al, Ti.
Ni-Fe alloys are precipitation-strengthened alloys that contain substantial amounts of Ni and Fe. They represent some of the most widely used superalloys and constitute their own class superalloys and constitute their own class. Primary emphasis is on age-hardenable alloys.
There are four groups of Strengthening Mechanisms such as :
- Group 1:Y’ strengthened as following:
- Fe-rich group (Ni = 25-35 wt.% + ~2 wt.% Ti)
- Ni-rich group (Ni > 40 wt.% + other elements)
- Group 2: Y’, strengthened (Ni-rich, Ni-Fe based),
- Group 3: Y’strengthened (Fe-rich Fe-Ni-Co based),
- Group 4: carbide, nitride, carbo-nitride strengthened.
- Group 1:Y’ strengthened as following:
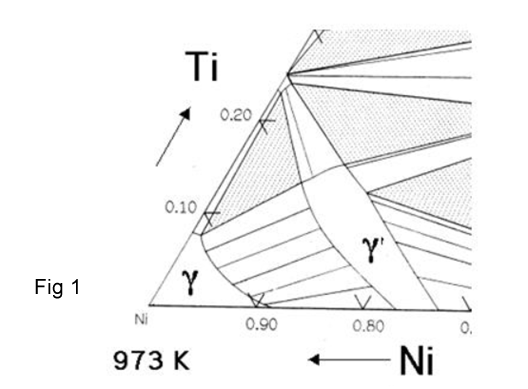
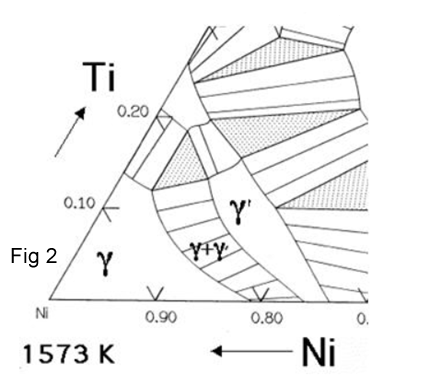