Blast Furnace (Technology)
The name is due to the fact that air is blown through the charge but it called shaft or vertical furnace (fig1), because it has a hearth and a stack .The furnace has the following characteristics:
- The charge consist of coarse iron ore, sinter, pellets , cokes and flux are entered at the top of the stack. The charge must be strong enough to withstand the static pressure in the shaft without crumbling into powder. Because during blowing powders will be blown outside the furnace by the gases. Powders can block the channels, which air must pass through them. This effect decreases the furnace efficiency.
- Cokes in the Blast furnace have two tasks; one task is the reduction process and the second task is heating, it is conducted by burning coke. It is ignited by air blown in the area of bottom of the furnace. The hot gases pass upward through the cold charge.
- Today furnaces have at the top the double bell system which keeps the furnace closed at all times duo to preventing the escape of gases even during charging .
- At the furnace high temperature can be used without damaging the refractory lining by inserting hollow wedge-shaped plates in the outer side of the refractory lining which are water-cooled.
- Aa large (1.5m) bustle pipe circular refractory –lined pipe through the bosh and upper part of the hearth wall. The blowpipe carries the hot blast from the bustle pipe through tuyere stock and gooseneck to the tuyeres. This section distributes the hot air to the furnace. The tuyeres are nozzle –like copper casting about 20 in number, spaced equally around the hearth about 30 cm below the top of the hearth. Each tuyere fits into a tuyere cooler casting through which cold water circulates.
- Between charge, air and gas are prevailed a counter-current heat exchange mechanism, the charge will be heated and the gas will be cooled.
- the molten iron and slag are settled in the bottom from where they can be removed
- the furnace is lined with refractory materials which must have a high melting point to withstand high temperatures. Alumina –silica refractories and Graphite are the most refractories substance.
- the weight of blast furnace could be 10,0000 ton and during the operation increased more than 5000 ton, therefore it must have strength foundation .To support a large furnace, a reinforced concrete pad about 3m thick and 18m diameter is built(fig4).A large furnace requires 8-10 supporting columns which are anchored to the concrete foundation.
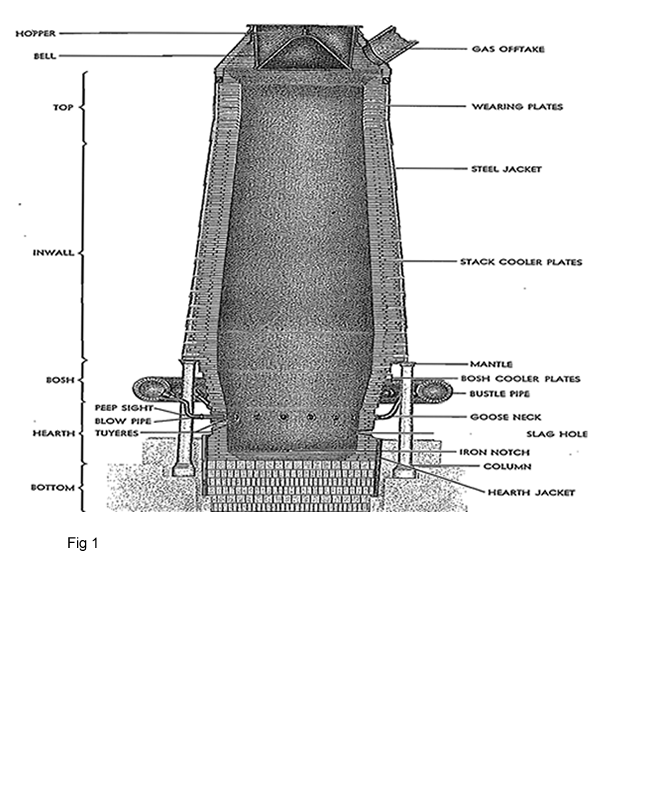
For more information please contact us.