Pelletizing
Pelletizing is the process of compressing or molding a material into the shape of a pellet. A wide range of different materials are pelletized such as chemicals and iron ore.
Iron ore Pelletizing
Iron ore pelletizing are made in two steps:
- Step 1: the Iron concentrate to be pelleted must have a sufficiently fine particle –size distribution (65-85 % less than 0.045 mm) and a specific surface area of at least 1600 cm2/g as measured by a permeability method (Blaine, Fisher Subsieve Sizer) Spherical green pellets (green balls) of appropriate size (ca 9-16 mm in diameter are formed by a pelletizing disk or drum. The particles are bound together by capillary forces acting through water bridges between them. This means that green pellets can be obtained only at a narrow range of moisture content. If the water content in the fine ore is too high, water-absorbent materials such as bentonite can be used to correct it within narrow limits.Figure 1 shows the Structure of porous agglomerate with reference to the relative distribution of air-water-solid phases. (a) Pendular (liquid trapped) (b) Funicular (air trapped) (c) Capillary (air expelled-liquid saturated)
- Step 2 the second operation is the thermal hardening of the pellets at 1200 -1320 0C.Nonthermal hardening is employed only in a few unimportant.Figure2 shows the process of the Pelletizing.
- The traveling grate
- The combination of preheating traveling grate rotary kiln (grate-kiln)
- Shaft furnace
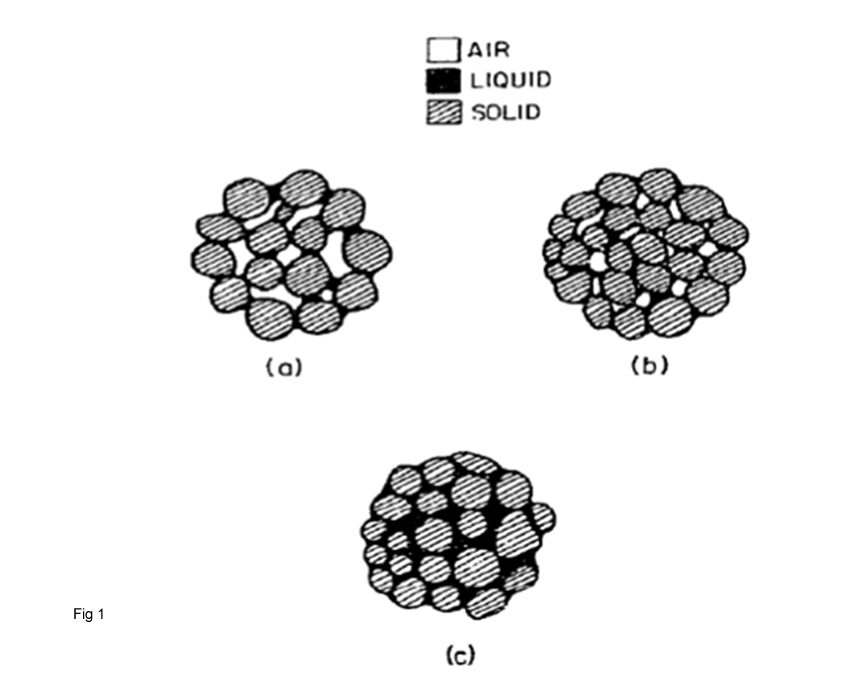
Prior to the formation of green pellets, substances are added to the fines to render them stable against the stresses that can occur in the hardening process.
There are three distinct heat hardening systems as following:
For more information please contact us.
