Material selection
Today a vast number of materials compete for their share of the market, with more new materials being added every year. Some particularly exciting developments are now occurring in the fields of ceramics, plastics and glasses and composites of these materials. The day of the ceramic car engine is probably not all that far off - already there is some high temperature components made from the new generation of tougher ceramics, and the modern motor vehicle also offers many examples of the use of engineering plastics. Recent developments in metals have re-asserted their competitive position in auto engineering, in particular the use of aluminium and magnesium alloys. A major revolution under way at present is the replacement of much copper telecommunications cabling with glass optical fibre. For metals to compete they must be able to demonstrate superior properties to their competitor.
Material selection is a step in the process of designing any physical object. In the context of product design, the main goal of material selection is to minimize cost while meeting product performance goals. Systematic selection of the best material for a given application begins with properties and costs of candidate materials. For example, a thermal blanket must have poor thermal conductivity in order to minimize heat transfer for a given temperature difference or, for a component that must support a specific load, the minimum yield stress that is required for the component’s material can be determined. This will be one of the material selection criteria.
Systematic selection for applications requiring multiple criteria is more complex. For example, a rod which should be stiff and light requires a material with high Young's modulus and low density. If the rod will be pulled in tension, the specific modulus, or modulus divided by density.
There are several situations during the life cycle of a product when a design team selects a material to use for a component or a joint between components. In addition to materials selection during new product development, companies also change materials to reduce costs, improve product performance and reliability, and improve manufacturing or assembly yields. Regardless of the situation, the goals are the same – find the lowest cost material that enables the product’s performance and reliability. There are several steps to the material selection process.
The materials selection process for a component or joint between components involves these steps:
- Identify the design requirements
- Identify the materials selection criteria.
- Identify candidate materials.
- Evaluate candidate materials
- Select materials
Material Selection Charts
In order to demonstrate the power of the material selection chart approach, a number of common property combinations have been plotted - these are listed below. If your browser is capable1, you should see interactive chart pages which:
- Allow you to view the selection charts
- Enable you to interactively 'explode' particular classes of materials
- Give brief definitions of the properties on the chart
- Provide general information about each chart and some insights into the physical reasons underlying it.
- Give examples of how each chart can be used in a design context.
- Set short easy questions involving each chart, with hints and brief answers
- Ask more involved questions about each chart that require greater 'lateral thinking' to solve - e.g. considering other charts as well, processing issues etc.
If your browser is not deemed capable of displaying the interactive version, you should automatically be given the non-interactive version. These charts contain most, but not all, of the features listed above. Figure 1 shows one of these charts, which give the information between Young's Modulus and cost.
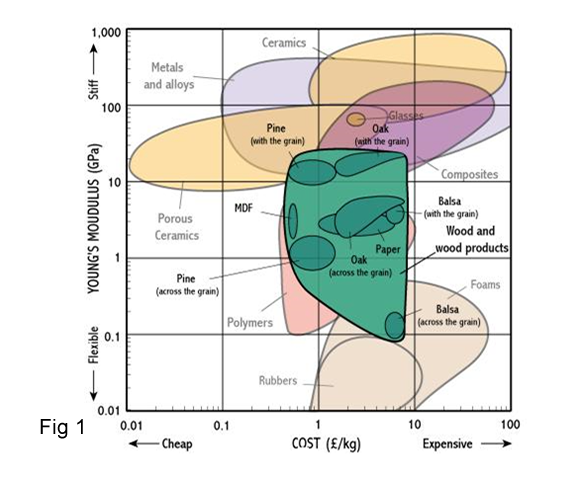
Young's modulus measures stiffness and is a material constant, i.e. it is the same whatever the size of the test-piece.
Many applications require stiff materials, e.g. roof beams, bicycle frames - these materials lie at the top of the chart.
Many applications require low cost materials, e.g. packaging foams - these materials lie to the left of the chart.
Cheap stiff materials lie towards the top left of the chart – mostly metals and ceramics.
ceramicsFor more information, please contact us