Stainless steel
Stainless steel is an alloy of Iron with a minimum of 10.5% Cr. Chromium produces a thin layer of oxide on the surface of the steel known as the 'passive layer'. This prevents any further corrosion of the surface. Increasing the amount of Chromium gives an increased resistance to corrosion
Stainless steel also contains varying amounts of C, Si and Mn. Other elements such as Ni and Mo are added to impart other useful properties such as enhanced formability and increased corrosion resistance. The addition of Ni to stainless steels improve their corrosion resistance in neutral or weakly oxidizing media but adds to their cost. Ni in sufficient amount also improves ductility and formability by making it possible for the austenitic (FCC) structure to be retained at room temperature .Mo, when added to stainless steel ,improves corrosion resistance in the presence of chloride ions ,whereas Al improve high temperature scaling resistance.
Chromium has the same Bcc structure as α ferrite therefore acts as a ferrite stabilizer and extends the phase field, while suppressing the γ-phase field. As a result, the “ γ loop” is formed, which divides the Fe-Cr into Fcc and Bcc regions (fig 1).
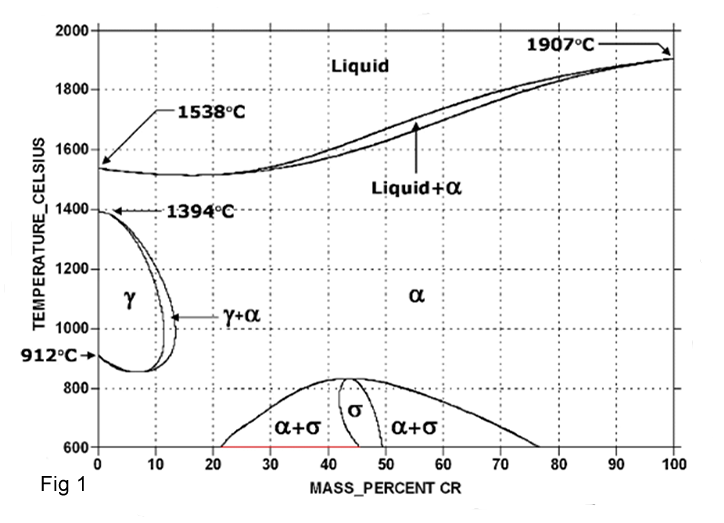
Iron – chromium alloys with less than 12 to 13 %Cr undergo an austenite-to ferrite transformation on cooling from temperatures within the γ loop. Iron – chromium alloys with more than 12 to 13% Cr do not undergo the Fcc to Bcc transformation, and on cooling from high temperatures remain as solid solution of chromium in α iron. Carbon is an austenitic stabilizer and when added to Fe-Cr alloys, enlarges the austenitic phase field.
The iron-chromium phase diagram at low temperature is not a complete range of solid solutions; an intermediate phase called the” σ phase “forms below 820oC, centered at about 46%Cr.The σ phase has a tetragonal crystal structure and is hard and brittle.
Iron-Chromium –Nickle –Carbon Alloys
When nickel is added to iron, it stabilizes the austenitic phase since nickel has the same Fcc crystal structure as austenite .Nickle is therefore an austenitic stabilizer in iron and counteracts the opposing ferrite-forming effect of chromium in stainless steel. If sufficient nickel is added to low –carbon stainless steel, the austenitic structure can be produced at room temperature. For example, a steel containing 0.2%C ,19.8%Cr and 4.4% Ni, after quenching from 1100oC,can produce an austenitic structure.
The most common austenitic alloys are iron-chromium-nickel steels and are frequently referred to as 300 series stainless. The best known austenitic Stainless Steel grades are 304/L & 316/L with other well-known grades such as 321 and 310. These grades contain minimum 16% chromium and 6% nickel commonly referred as 18/8 stainless (grade 304). Austenitic grades are generally preferred for their ease of fabrication resulting from a stable metallurgical microstructure at all temperatures combined with good corrosion resistance, mechanical and physical properties.
The addition of molybdenum to a steel containing 18% chromium and 8% nickel improves corrosion resistance and increases significantly the high temperature strength. Grade 316/L is the most common example of this.
Included is the high alloys or “Super Austenitic” with increased chromium and nickel such as 904/L & 310/L containing up to 26% chromium and 22% nickel. Ideal for high temperature use with excellent corrosion resistance to strong acids and chlorides.
For more information, please contact us