Copper
Copper is an important engineering metal since it is widely used in its unalloyed condition as well as in alloys with other metals. It has an extraordinary combination of properties which make it the basic material in the electrical industry. The important application of copper is electrical industry. Copper alloys are metal alloys that have copper as their principal component. They have high resistance against corrosion.
Physical Properties of Copper (table1)
Table1
PROPERTY | VALUE | UNITS | PROPERTY | VALUE | UNITS |
Atomic number | 29 | - | Atomic weight | 63.54 | - |
Crystal structure | Fcc | - | Atomic radius | 1.277 | Ao |
Density of copper | 8.92 | g/cm3 | Melting point | 1083 | oC |
Boiling Point | 2595 | oC | Latent Heat of Fusion | 205 | J/g |
Specific Heat at 20 oC | 0.386 | J/g °C | Thermal Conductivity at 20 oC | 3.94 | Wcm/cm2 °C |
Electrical Conductivity at 20oC | 100-101.5 or 58-58.9 | %IACS or m/mm2Ω | Modulus of Elasticity at 20 oC | 118,000 | MPa |
The Effect of Impurities on Conductivity of Copper
Most coppers used for electrical transmission and interconnection have electrical conductivity of 85% IACS or greater. Commercially pure copper has 101% IACS . As do several of the oxygen free (pure) coppers like C10100 and C10200. The electrical conductivity of copper will decrease with an increase in impurities. Figure 1 shows the negative effect of different elements on the electrical conductivity of copper. For instance when, when residual P is high, the electrical conductivity is drastically reduced.
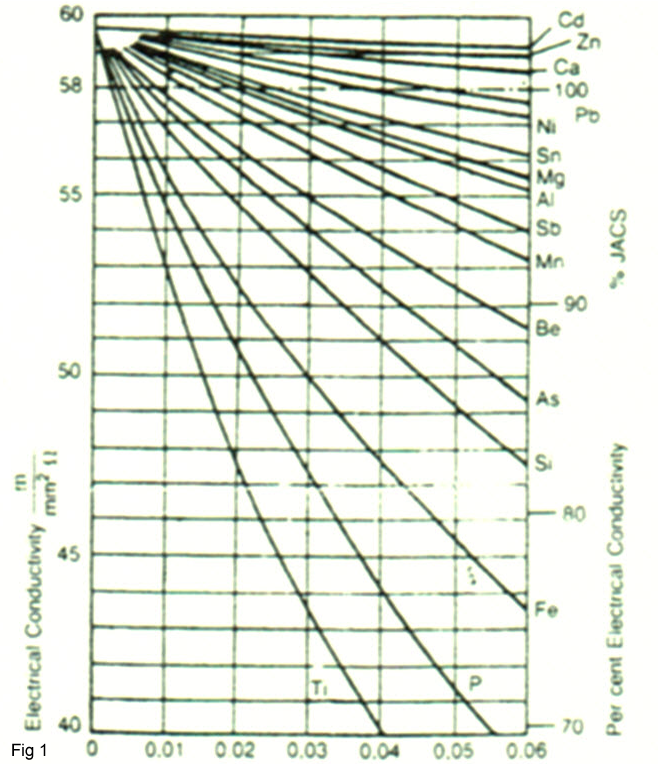
Classification of copper and copper alloys
The Classification of copper is as following:
- Unalloyed copper
- Brass
- Bronze
- Cu –Ni based
Copper –Zinc alloys –Brasses
Copper –Lead alloys –Alloy brasses
Copper –Zinc alloys with Tin and Aluminium additions
Cu-Sn alloys
Cu –Al alloys
Cu-Si alloys
Cu -Be
Cupronickel (Cu-Ni)
Nickel silver (Cu-Ni-Zn)
Copper and copper alloys are identified by the Unified Numbering System (UNS) which categorizes families of alloys based upon their elemental make-up. Wrought products range from UNS C10000 through UNS C79999; cast products are assigned numbers between UNS C80000 and UNS C9999 as following (table 2):
Table2
Wrought Alloys | Cast Alloys | Wrought Alloys | Cast Alloys |
Coppers (C10100 - C15999) | Coppers (C80000 - C81399) | High Copper Alloys (C16000 - C19999) | High Copper Alloys (C81400 - C83299) |
Brasses (C20000 - C49999) | Brasses (C83300 - C89999) | Bronzes (C50000 - C69999) | Bronzes (C90000 - C95999) |
Copper Nickels (C70000 - C73499) | Copper Nickels (C96000 - C96999) | Nickel Silvers (C73500 - C79999) | Nickel Silvers (C97000 - C97999) |
- | Leaded Coppers (C98000 - C98999) | - | Special Alloys (C99000 - C99999) |
The Wrought Coppers
Unalloyed copper is an important engineering metal. Because of its high electrical conductivity, it is used to a large extent in the electrical industry. Other properties such as high thermal conductivity, high corrosion resistance, good ductility and malleability and reasonable tensile strength make unalloyed copper attractive as an engineering material. There are three types of important unalloyed copper as following:
- Electrolytic tough-pith copper
- Oxygen-Free Copper
- Deoxidized Coppers
This copper has a minimum of 99.9 % Cu and 100 -500 ppm Oxygen content and is used more for the production of wire, rod, plate and strip. Oxygen is almost insoluble in copper, as shown in Cu-O phase diagram of Figure 2 interdendritic eutectic upon solidification. This figure shows the interdendritic eutectic Cu2O in as-cast electrolytic tough-pith copper. Figure 3 shows the microstructure of the Cu2O particles.
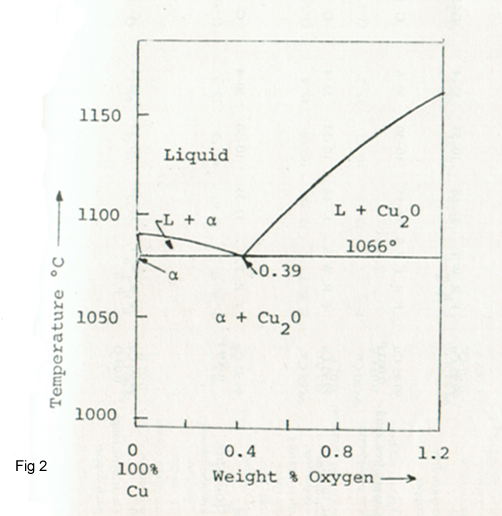
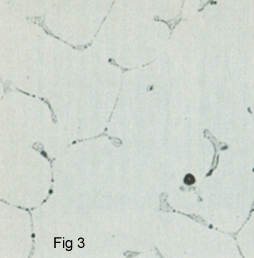
Tough pith copper cannot be used where joining process involve temperature above 400 0C. Because of the following reaction:
Cu2O + H2 = Cu + H2O
By using H2 as reducing Gas during joining process .Since the hydrogen atoms are so small, they are able to diffuse into the solid copper and react with Cu2O particles to form steam according the above reaction. Since the steam formed by the reaction is insoluble in copper, high pressures build up so that grain boundaries of the copper rupture. During melting Process, because H2O is not soluble in the copper. This leaves a porous structure (fig 4). This effect is characterised as Hydrogen embrittlement.
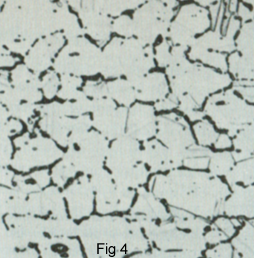
Oxygen-free copper can be produced from cathodic copper by melting and casting under a reduction atmosphere of CO and N2 so that oxygen is prevented from entering the copper. The as-cast structure of oxygen-free copper (99.95%Cu) does not contain the interdendritic eutectic Cu2O and gas porosity (fig 5).The Oxygen-free copper is not susceptible to Hydrogen embrittlement at elevated temperature.
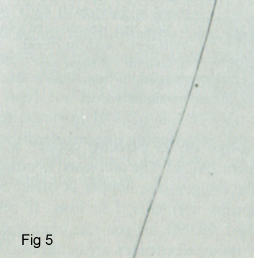
With the addition of sufficient phosphorus or Calcium hexaboride (CaB6) all the available oxygen in the copper will be removed.
Copper zinc alloys (brasses)
The Copper zinc brasses consist of a series of alloys of copper with up to about 40% Zn. As the percentage of Zn changes, the properties of the Cu-Zn alloys change too. The best combination of ductility and strength occurs at 70 % Cu and 30 % Zn, and hence this alloy can be used for its excellent deep-drawing ability. This alloy called cartridge brass but is used for other applications.
The Phase diagram Cu-Zn is shown in figure 6, where it is seen that the maximum solubility of zinc in copper in form α (Fcc crystal structure) is about 38% and at 20 0C it is about 35%. With increasing zinc content, a second solid solution of zinc in copper in form β (Bcc crystal structure) is occurred. The β phase transforms upon cooling through the 468 to 456 0C temperature range from a disordered β phase structure to an ordered β' structure. With more than about 50% Zn, the γ-phase solid solution forms,which has a complex structure and which is very brittle. Cu-Zn alloys containing the brittle γ-phase are of little engineering use.
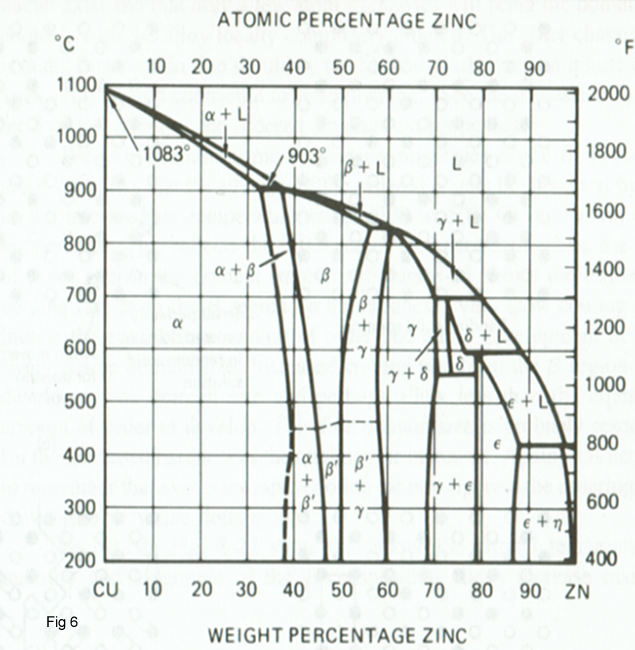
On the basis of the Cu-Zn phase diagram, commercial brasses can be divided in two important groups:
- α brasses with the structure containing up to about 35% Zn.
- α+ β brasses with the α+ β two-phase structure, which are mainly based on a 60/40 ratio of copper to zinc.
For more information please contact us